IADC ART Spark Tank
Holly Shock
IADC ART Spark Tank Meeting
Date: 24 April 2019
Time: 8:30 – 11:30 am
Venue: IADC
Location:
(Please note our new address)
3657 Briarpark Drive, Suite 200
Houston, TX 77042
Contact: Holly Shock
Phone: 1-713-292-1945
Email: holly.shock@iadc.org
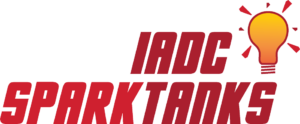
Register now to attend IADC ART Spark Tank at IADC’s new Houston headquarters
Register to hear new ideas on diverse topics at the next IADC Advanced Rig Technology (ART) Spark Tank, scheduled for 08.30-11.30 on Wednesday, 24 April 2019. The Spark Tank will convene at IADC’s headquarters at 3657 Briarpark Drive, Suite 200, Houston, TX 77042
The event provides an opportunity to technology entrepreneurs to pitch their products and ideas (“Sparks”) to a panel of drilling contractors and operators (“Sharks”). The purpose is to give insights to technology developers into what matters to those for whom they are innovating. Only Sharks will ask questions of the presenters. Audience members are welcome to chat with presenters during the break and following adjournment.
IADC is grateful to its Sharks for sharing their time, talents, and expertise. Sharks for the 24 April Spark Tank are:
-
Craig McCormick, Transocean, Senior Manager Innovation
-
Rob Shank, Parker Drilling, Senior Director Global Drilling Operational Excellence, and ART Vice Chair
-
Matthew White, Apache Corp, Drilling Engineer
-
Robert van Kuilenburg, Noble Drilling (ART Chair and moderator)
Agenda
9:00 Welcome & Introductions – Robert van Kuilenburg, IADC ART Chair
Speakers have 15 minutes, with 15 minutes allotted for Sharks’ Q&A:
9:15 “LaserStream: Laser Profiling the Inside of Tubular Assets”: Jason Waligura, LaserStream
LaserStream has introduced the Bore Erosion Measurement & Inspection System (BEMIS) laser scanning technology to the oilfield. Current focus includes drilling and workover risers, frac erosion and failed casing. The BEMIS laser sensor rotates at a high rate of speed as it is driven the length of a tubular, typically generating upwards of 5,000 data points per revolution. The result is a high-resolution 3D map of the component inner surface. The linear resolution can be as tight as 0.010 in. or as loose as 5 in., depending on the application. For example, a 40-ft joint scanned at 0.5-in. resolution gathers over 2.4 million data points. This data provides information about wall loss (erosion, corrosion), mechanical wear (wireline, coil tubing), ovality, and exact dimensions and volumes. Typically, depth and sizing measurements are accurate to +/- 0.002 in. or better. Until recently, this technology has been primarily used by organizations such as NASA, nuclear power companies and for Department of Defense gun turret erosion inspection applications.
9:45 “Getting Twisted Over Bolts: A Viable Option for Threaded Metallic Fasteners”: Brandon Carringer, Whitefield Plastics
Complex fastening technology, such as metallic threaded bolts and components, has created the need for innovative fastening solutions. Material traceability, material degradation, exotic material costs and localized surface area force become challenges with alternate materials. Bolting systems were analyzed to determine the viability of replacing steel bolting systems with polyurethane connection systems. Requirements during development were for a single-piece connection system made from polyurethane technology, satisfying traditional metallic, threaded bolt material properties, performance, safety and cost. Initial prototypes highlighted the need to pay close attention to component relative size, as the total elongation of a stressed member increases proportionally with length. Multiple iterations revealed a functional necessity for engineered components that use interference fit features, thus generating preload (similar to the functionality of a bolted connection). The engineered solution is relatively compact, preloaded upon installation, and features distributed surface contact stresses along the length of the system. The combination of these features create a nonmetallic system that, in some cases, outperforms threaded fastening system loads and surpasses metallic system life expectancy in hostile environments.
10:15 Break
10:30 “igus iSense Remote Energy Chain Monitoring System”: Jason Freed, igus
Rig automation and remote monitoring has faced challenges in reliability, but what if we can predict failures before they happen? With the igus iSense remote monitoring systems, the operator can continuously monitor the energy chain during operations and plan system maintenance. The system can provide feedback on chain wear, excessive force parameters (push/pull), breakage detection and cable conductor health. If a failure is imminent, the system can also trigger a full stop to avoid a costly repair or extended downtime on the rig. The system is easily implemented in control junction boxes and can be used on top drrive motion, pipe-handling operations, BOP wranglers or catwalk systems.
11:00 Design Changes Addressing Measurement Limitations of Orifice flowmeters: Zaki Husain, ZS Technology
The experimental results of orifice meter pressure distribution and geometrical influences of the orifice plate of the orifice meters have led to imposed limitations of the mechanical and theoretical tolerances in the orifice meter standards. Based on the observations and findings of those experimental results, a modified primary element for the differential pressure generating device was developed. The experimental results of that device will be discussed, as well as how the orifice meter mechanical tolerances can be relaxed. With the new device, flow rate measurement by the modified differential pressure generating primary element can significantly improve the flow rate measurement and offer stable and reproducible meter performance. This modified device can further improve the manufacturing constraints by limiting the area ratio to a limited number of only about three beta ratios.
11:30 Adjournment
Photos and Videos are not permitted at this event without the express permission of IADC.